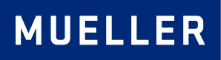
PMC MilkSecure IIoT Platform and Control System
Paul Mueller Company is cooling the world’s milk. By working with dairy farmers, technicians, haulers, and processors throughout the dairy supply chain they provide tailored solutions to cool and store milk. At the heart of each solution are stainless steel tanks made in America and The Netherlands, and shipped to any place cows are milked.